LGS
Structure.
BYLD’s LGS Framing solution is an end-to-end platform that transforms stock, cold-rolled steel into a fully compliant LGS structure – on-site or wherever you choose to produce your components. It eliminates the improvisations, waste and delays involved in traditional carpentry by creating a precise match between the 3D model and the finished part, from wall sections to open web trusses to headers and sills.
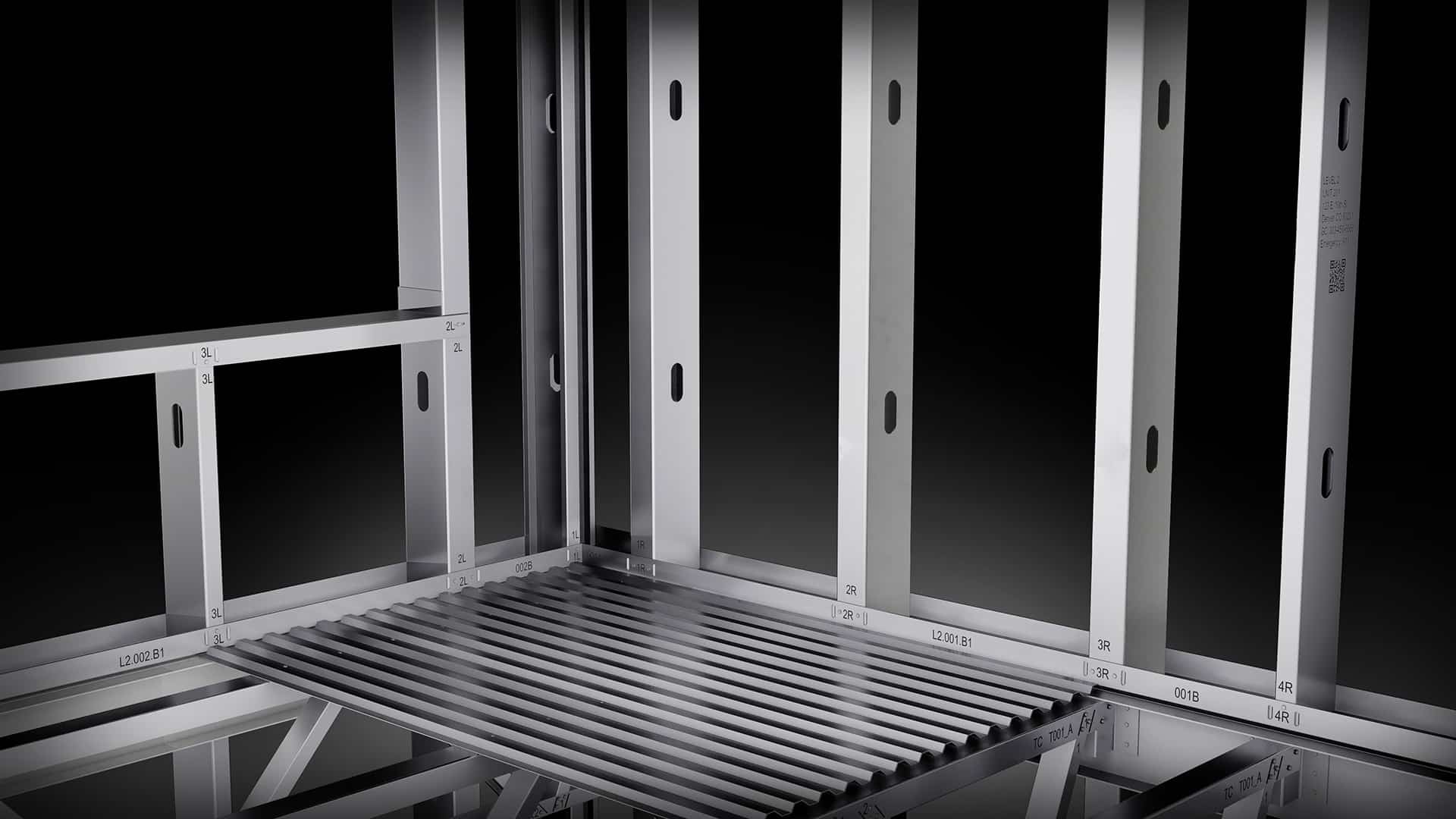
Reduce Your OpEx and CapEx
With BYLD Framing Equipment.
BYLD framing cells can be deployed as a complete system for processing and assembling LGS frame elements – walls, trusses, beams and more – or in any combination, to solve specific LGS framing challenges.
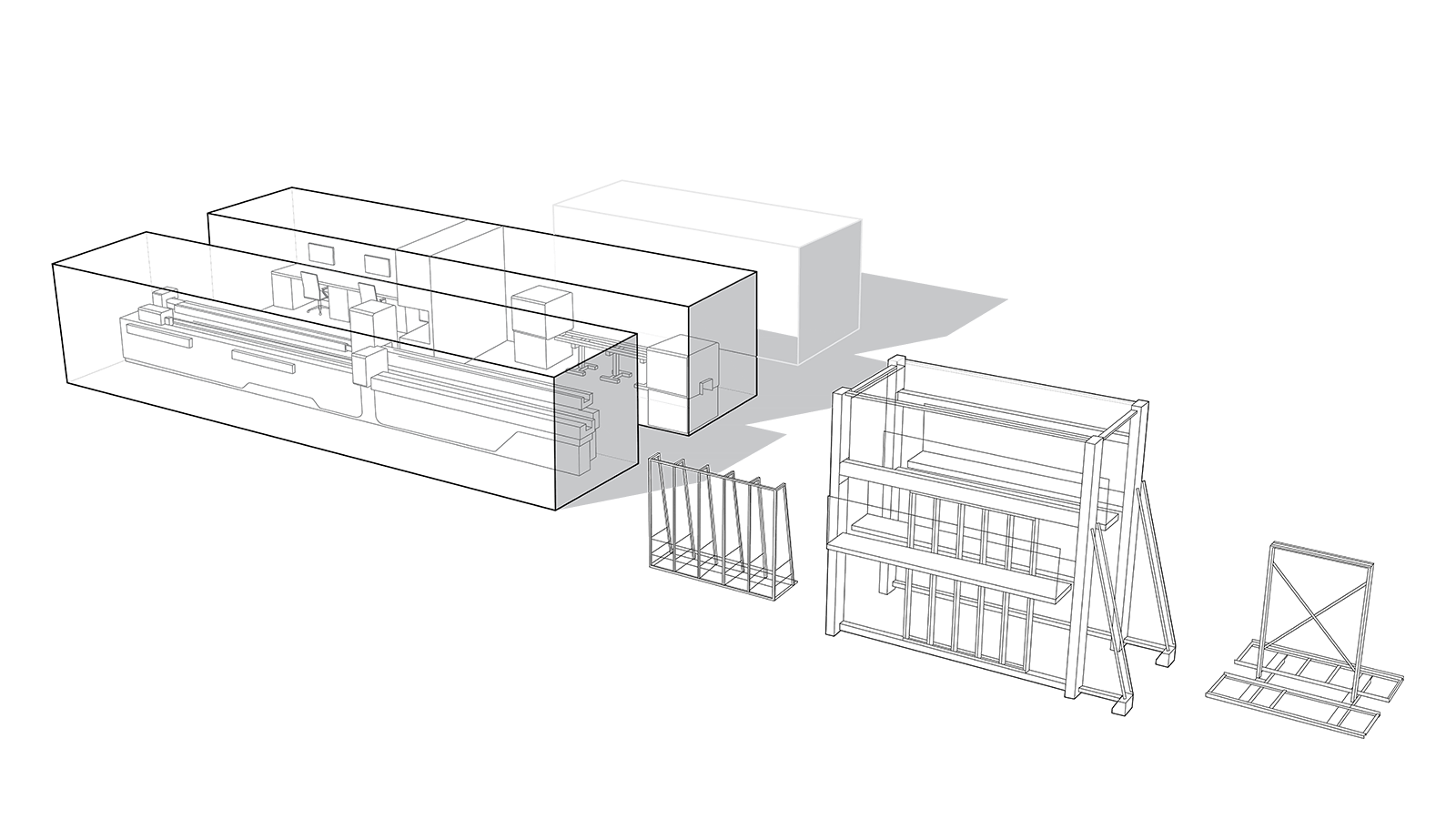
Structural framing.
Precision automation eliminates the carpenter-centric approach to wall section framing. Processing each framing member to size and laser etched for quick assembly. No plans, no measuring, no margin of error.
Strapping.
When there’s a need for LGS X-brace strapping there is no simpler solution. Eliminate the traditional time consuming and wasteful approach.
Header & Sill.
Don’t hope that framed opening meet the specs of the windows, doors and building openings. Eliminate interpretation and BYLD by Numbers™.
Field office.
Integrated field offices give technology-based command and control of supply chain and project management.
Jig.
An innovative approach to wall framing enables manufactured precision to the process of carpentry. Guided by BYLD by Numbers™ – no interpretation, no flipping. Faster and safer.
BYLD Structure
Process.
BYLD software solves the architect’s plan into a fully engineered structure automatically, then delivers a set of detailed digital instructions to BYLD hardware cells for streamlined, fully-contained production. What emerges on the back end is a series of industry-standard LGS components, processed in a fraction of the time with minimal waste and less variability, ready to assemble with less skilled labor required.
One // Automated Engineering Analysis of Architect's Plan
BYLD’s REVIT-based software application makes 3D modelling fast and precise. And BYLD’s engineering application automates the process of engineering design.
Two // Populate Building Layout With Optimized LGS Structure
The structure is then populated with industry-standard LGS framing materials, optimized to reduce cost.
Three // Automated Production of Precise Bill of Materials
BYLD software automates takeoff of a precise bill of materials, reducing the need to estimate and cutting material contingencies.
Four // Convert Bill of Materials to PO and Machine Files.
Material scheduling and purchasing is linked from vendor to contractors through the BYLD Portal. A seamless supply chain solution.
Five // Process Materials for BYLD by Numbers™ Assembly and Installation
Framing materials are Laser-etched for a BYLD by Numbers™ approach to assembly and installation, reducing time and labor.
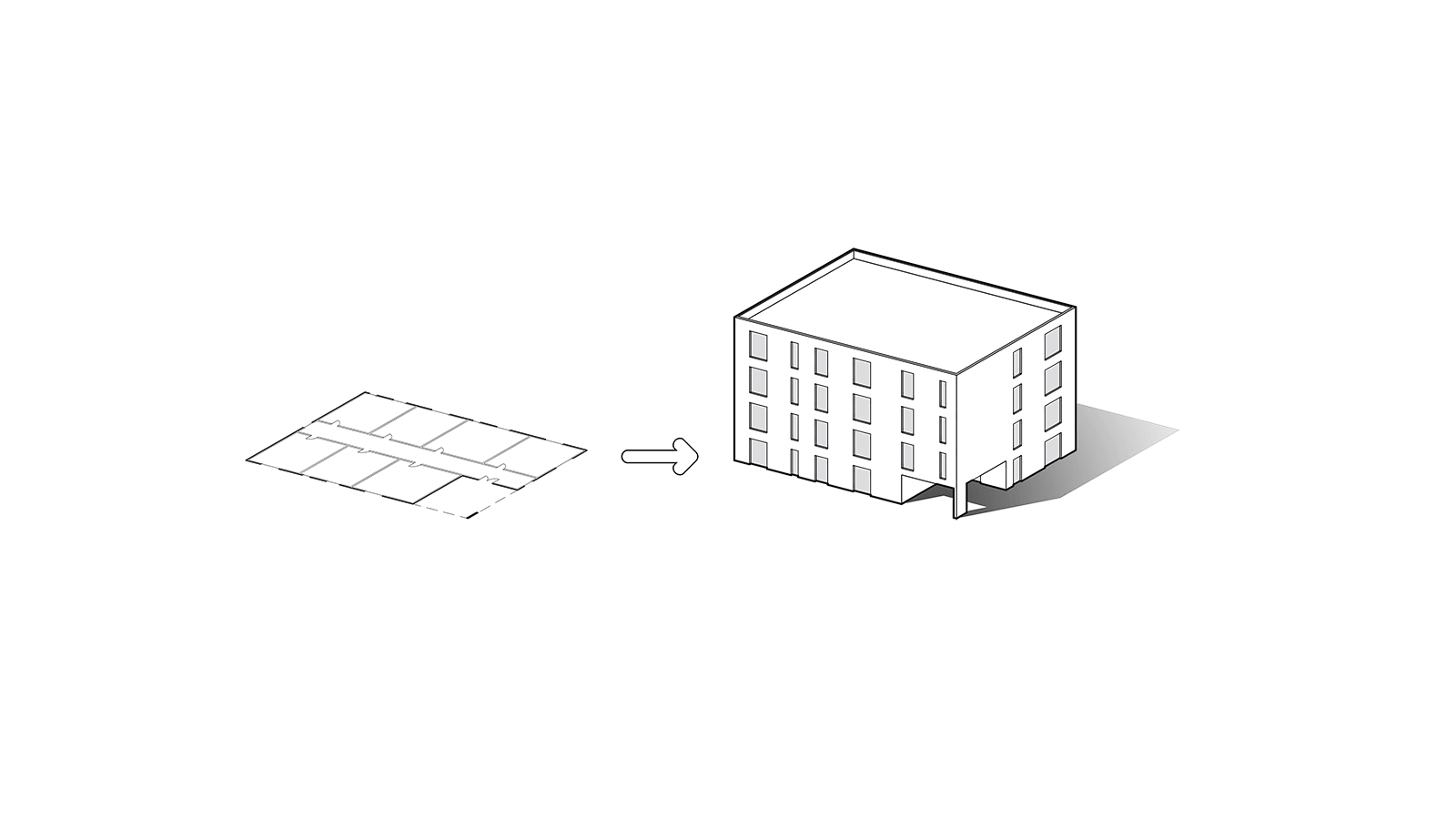
Benefits.

Lower Costs
$15 to $20 less per square foot than concrete and traditional light gauge steel structure, and cost-comparable to wood without the waste and labor demands.

Twice the Throughput
Finish 20,000 sqare feet per week versus 10,000 square feet per week with traditional stick framing.

50 percent less labor
Requires half the labor overall of traditional stick framing and 90 percent less skilled labor.

Universal Adoption and Compatibility
BYLD components are standard and non-proprietary, engineered for compliance with IBC and local codes.

Lower insurance costs
BYLD Type I and Type II structures are 50-90 percent less costly to insure than wood structures.

Zero waste
BYLD hardware cells process components to precise specifications from BYLD software, reducing waste; LGS has a 99.5 percent efficiency factor because it is fully recyclable.

Safer structures
BYLD LGS components are non-combustible, dimensionally stable, and capable of delivering 100-plus-year structural durability and reduced maintenance.

Built green
BYLD solutions are engineered to minimize environmental impact and improve your project’s green profile.