LGS
Trusses.
BYLD open web trusses are generic and UL certified, having passed a two-hour fire test. With BYLD’s integrated truss solution the complex job of manufacturing trusses gets much simpler, faster and less costly. Guided by BYLD software, the BYLD Truss Cell delivers the consistency and higher productivity of a manufacturing environment without sacrificing flexibility. Installing BYLD’s integrated Truss solution in your plants lets you produce any required length and depth to meet your project requirements without time-consuming changeovers. The Cell adjusts all metal-forming and finish operations on the fly, in response to precise instructions from BYLD software. And the containerized BYLD Truss Cell can be deployed anywhere in the world, speeding turnaround and enabling just-in-time delivery to customer sites.
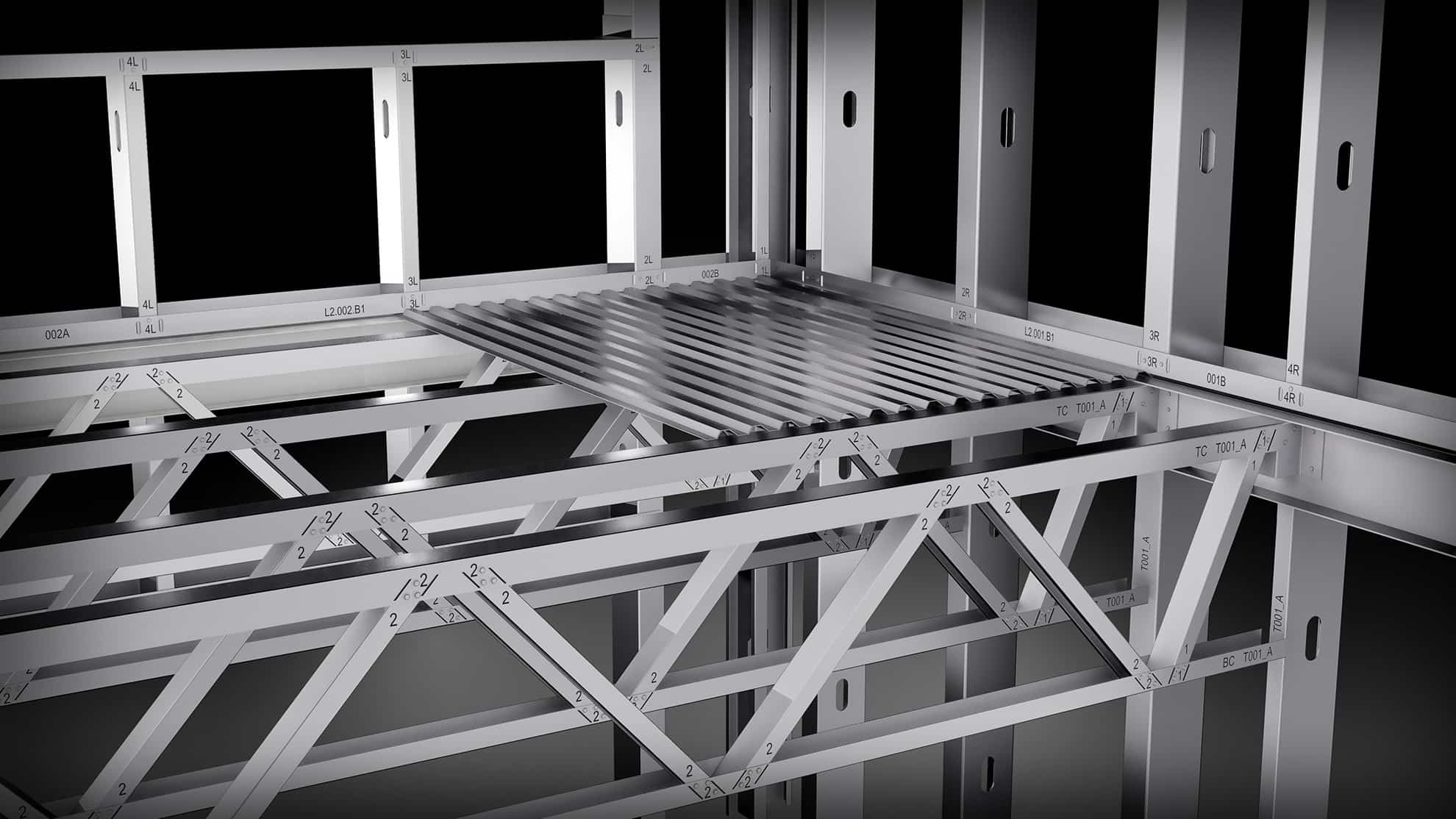
Truss manufacturing.
BYLD’s integrated truss manufacturing solution is portable and vastly simplifies the process. Digital plans are interpreted into truss components that are assembled in BYLD’s vertical jig. No plans, no measuring, no guesswork, saving time and money compared to conventional approaches.
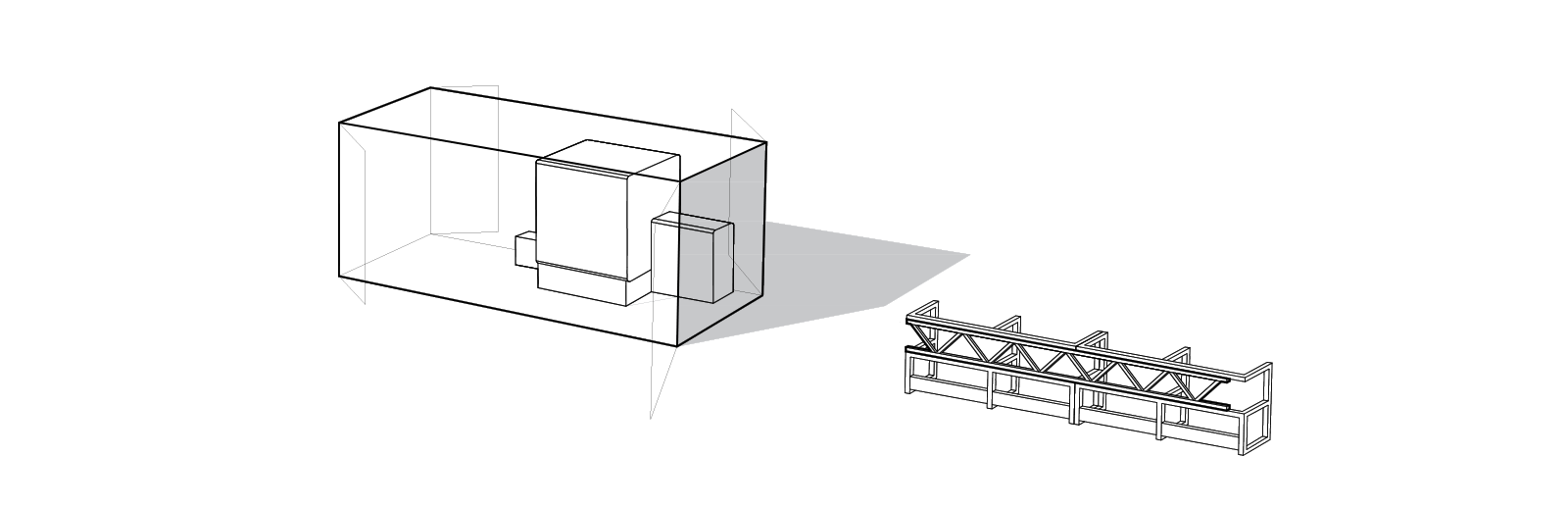
Automated Truss Manufacturing.
A Proprietary machine that interprets web and chord requirements from the plans and processes each piece for assembly. A completely different way to build open web trusses – faster, simpler, and safer.
Truss Assembly Jig.
Vertical, BYLD by Numbers™ assembly. Finally, a better solution to build open web LGS floor and roof trusses. Reduces cost and makes LGS a competitive solution.
BYLD Truss
Process.
One // Automated Analysis of Floor Layout
BYLD’s proprietary Autodesk REVIT plug-in application allows for fast, accurate modeling and analysis of the floor structure.
Two // Floor Load Analysis To Size and Design Trusses
BYLD software analyzes floor loading using code-based criteria to size and design trusses.
Three // Automated Conversion of Design Data to Machine Files
Linking design to processing via BYLD’s software conversion engine – seamless, automated integration.
Four // Machine Processing of Truss Webbing and Chords
Each chord and web is cut to size and laser etched for quick assembly in BYLD’s truss jig.
Five // BYLD by Numbers™ Guides Assembly
Laser etched parts guide the assembly. BYLD by Numbers™ changes the way you assemble trusses, saving time and money.
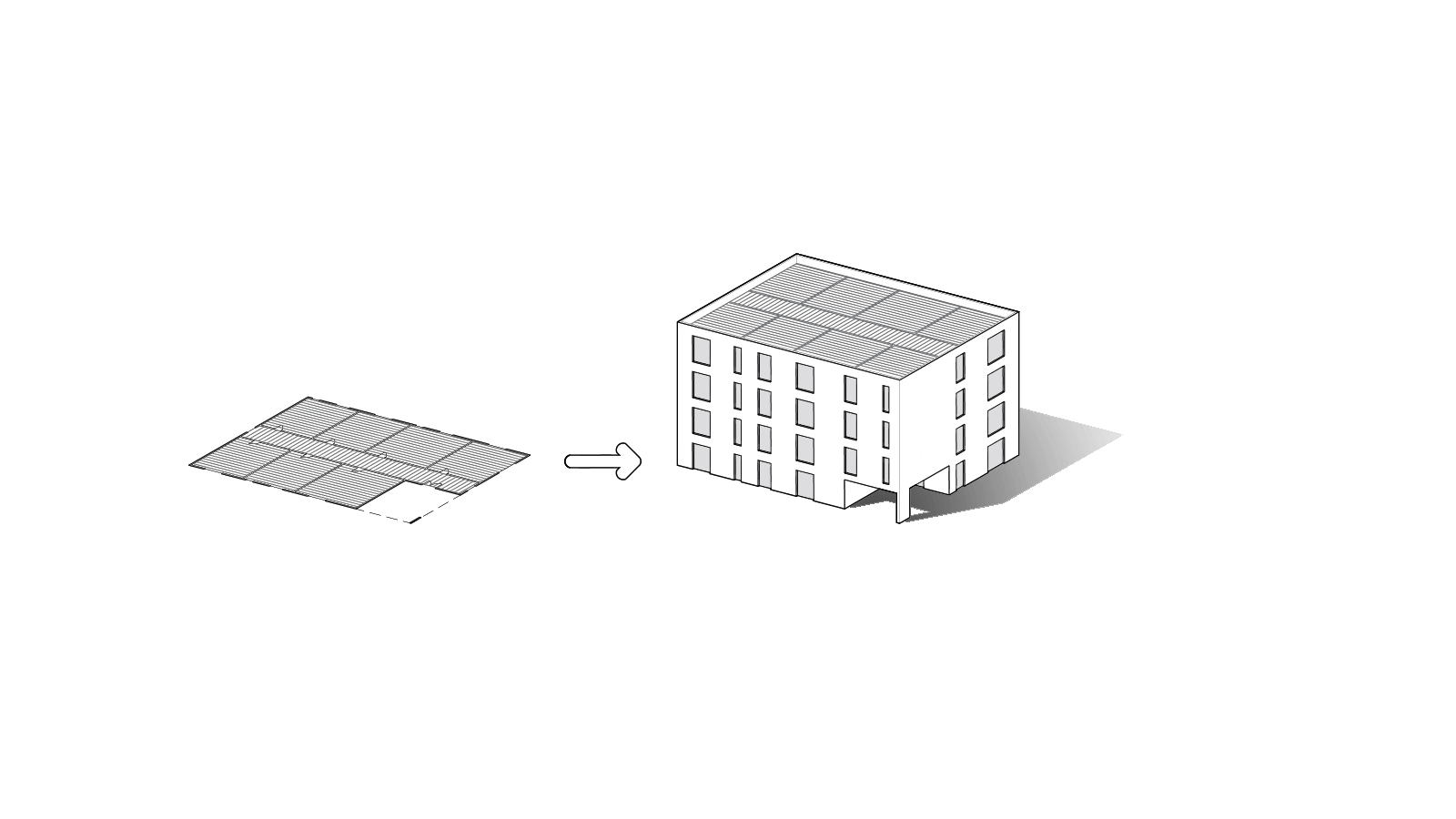
Benefits.

Lower Costs
$15 to $20 less per square foot than concrete and traditional light gauge steel structure, and cost-comparable to wood without the waste and labor demands.

Twice the throughput
Finish 20,000 sqare feet per week versus 10,000 square feet per week with traditional stick framing.

50 percent less labor
Requires half the labor overall of traditional stick framing and 90 percent less skilled labor.

Universal adoption and compatibility
BYLD components are standard and non-proprietary, engineered for compliance with IBC and local codes.

Lower insurance costs
BYLD Type I and Type II structures are 50-90 percent less costly to insure than wood structures.

Zero waste
BYLD hardware cells process components to precise specifications from BYLD software, reducing waste; LGS has a 99.5 percent efficiency factor because it is fully recyclable.

Safer structures
BYLD LGS components are non-combustible, dimensionally stable, and capable of delivering 100-plus-year structural durability and reduced maintenance.

Built green
BYLD solutions are engineered to minimize environmental impact and improve your project’s green profile.